Uruguay is opening the door to a sustainable transition in its construction sector. Having led the way in Latin America in transforming its energy mix over the past two decades – with 94% of its electricity generated by renewables between 2017 and 2021 – it is now laying the foundations for another sustainable shift, this time towards high-rise timber buildings.
Two recent developments have boosted the sector: the construction, in Uruguay, of South America’s first plant manufacturing cross-laminated timber (CLT) – an engineered wood product seen by many as a sustainable alternative to concrete and steel – and the government’s announcement of a “roadmap” for the construction of social housing using timber frames.
However, realising a wider shift will face challenges. The government will need to align current building regulations, though changes have already been introduced and others are being prepared. It will also need to involve industry, professionals and academia, to train workers and link the sector to national and global environmental policies. But with construction accounting for 9% of Uruguay’s carbon emissions (without taking into account emissions from construction-related transport), overcoming these challenges could help the country make significant further steps towards its 2030 net-zero target.
The case for timber in Uruguay
Though wood has been a building material throughout history, from the Industrial Revolution onwards, the use of iron, glass, steel and, later, cement began to dominate, with wood being more vulnerable to water, fire and insects. Today only 18% of the world’s population lives in timber housing – and much less is used in the construction of public, commercial, industrial and office structures.
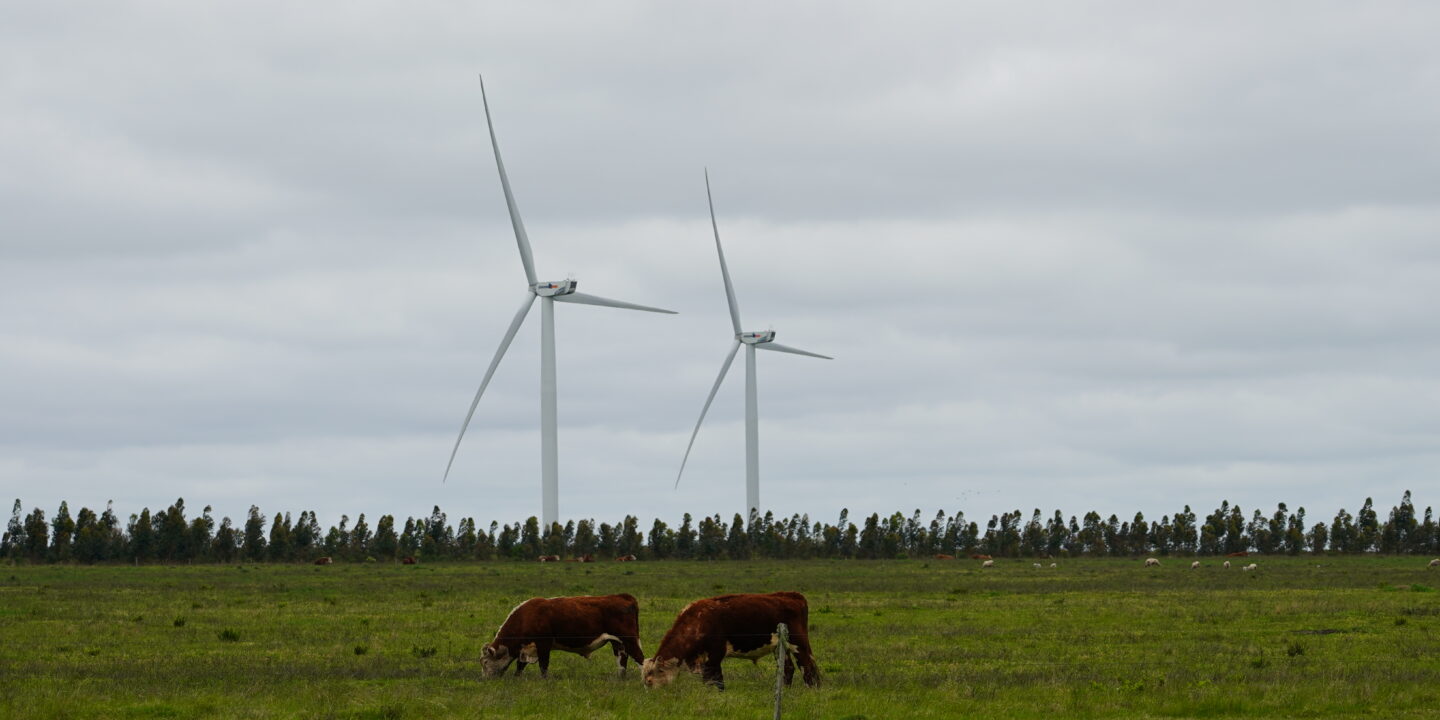
Modern materials made it possible to build larger and taller structures, but the whole cycle of production, transport and construction has relied on heavy use of fossil fuels. A tree, however, works in reverse. It sequesters carbon as it grows and can be made into timber using much less polluting industrial methods.
Compared to other products made from non-renewable or emissions-intensive materials (such as cement or steel), wood products are responsible for fewer greenhouse gas emissions over their entire life cycles. For every kilogram of carbon from wood products used in construction to replace non-wood products, an estimated 1.2 kg of carbon emissions may be avoided, according to an academic review led by the European Forest Institute..
Elsewhere, according to a study by Yale University and the University of Washington, “using wood substitutes could save 14% to 31% of global CO2 emissions and 12% to 19% of global fossil fuel consumption by using 34 to 100% of the world’s sustainable wood growth.”
In Uruguay, where electricity generation is almost entirely based on renewables, a sawmill’s energy consumption to produce timber building materials is likely supported by hydroelectric, wind, solar and biomass generation.
What is cross-laminated timber (CLT)?
The development of cross-laminated timber (CLT) began in Austria in the 1990s, and the material has since been able to support 25-storey buildings, while its fire risks have been reduced, and its resistance to moisture and pests enhanced. This year saw the opening of an 86.5-metre tower block in the United States, which surpassed another in Norway to become the world’s tallest CLT-framed building.
CLT panels are made from multiple layers of dried spruce or pine boards – typically three, or another odd number – crossed at 90 degrees and glued together, and made to measure for each building project. Panels can then be assembled in Lego-like fashion. They are used as structural elements, such as interior walls, slabs, columns and beams, as well as facades, and integrated with glass, aluminium and other materials. They allow for greener, faster, cheaper and cleaner construction.
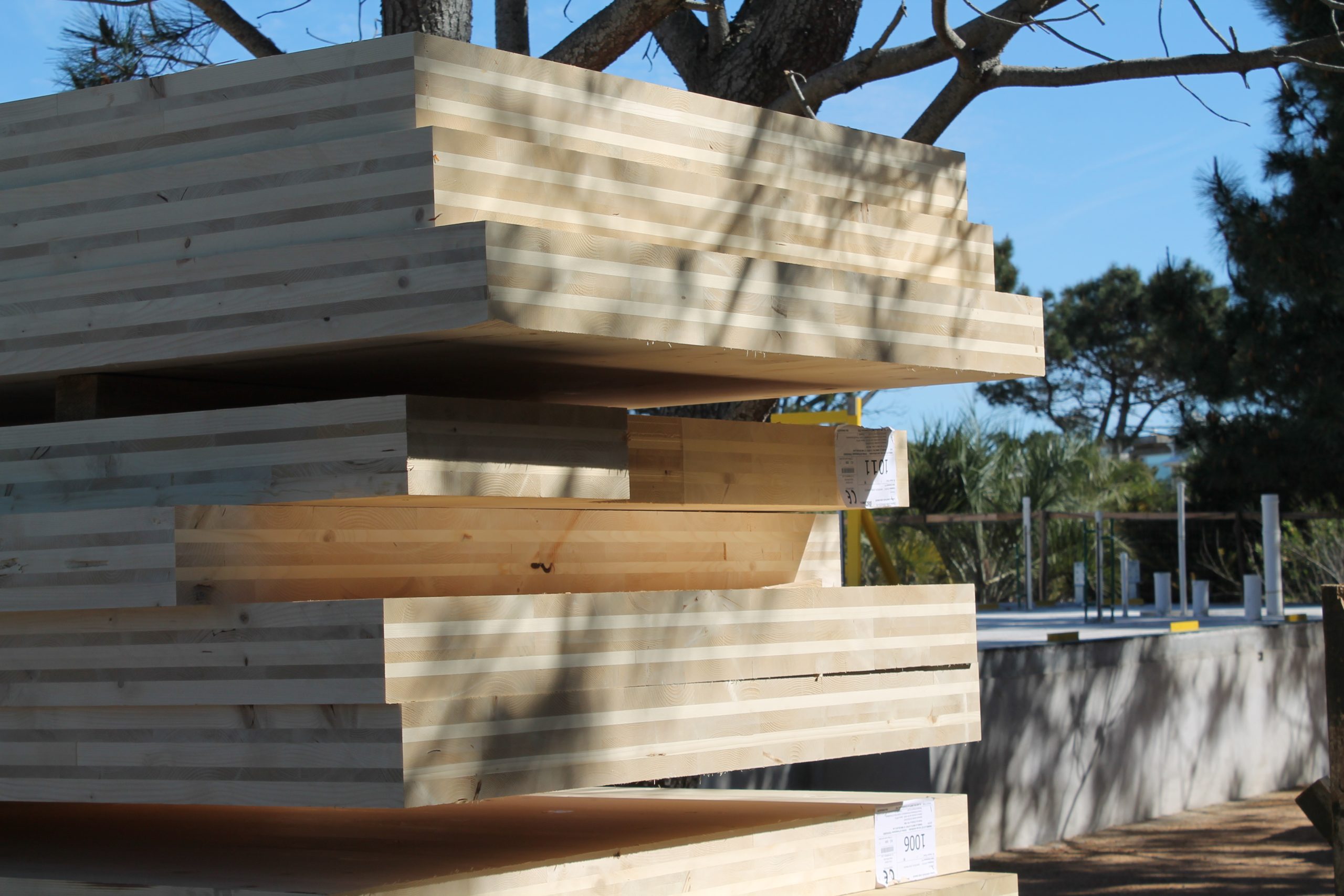
CLT panels have environmental advantages across their whole cycle, from the production of trees to the industrial process, transport, on-site assembly and energy consumption of the resulting buildings, associated with the insulating capacity of wood versus other materials.
CLT is widely reported as being up to five times lighter than concrete or brick, meaning more materials can fit into a lorry than those needed for traditional construction, reducing carbon emissions at the transport stage. The use of CLT also reduces the amount of waste generated on construction sites.
To erect a 20-storey concrete and steel building, roughly 1,215 tonnes of carbon are emitted in the construction and transport of the materials, according to American architect and wood building expert Michael Green. The same building made with wood could sequester 3,150 tonnes of carbon during the growth of the trees used to construct its panels.
Added value to the pine industry
The building of the largest CLT plant in South America in Uruguay would increase the availability of an input that is otherwise scarce in the region, for both the local and regional markets, boosting supply of a material that will be necessary in the larger-scale transformation of the construction sector.
In April 2021, Uruguayan businessman Matías Abergo partnered with US-based investor Mike Crandall to buy the Frutifor sawmill, in the northern department of Tacuarembó, for US$25 million. They founded the company Arboreal and committed another US$34 million to transform it into a CLT plant, which will reportedly begin production by December 2022.
Crandall is a former oil entrepreneur, who claims to be repenting for “past misdeeds” having made his fortune in fossil fuels. In the 1980s, he was an oil trader for Morgan Stanley and Glencore, before co-founding oil giant Trafigura Group in 1993.
But in 2006, he moved into green energy. He set up Postscriptum, a venture capital group that invests in renewable energy. Crandall bought a house in Punta del Este, in eastern Uruguay, that was in need of renovation. He hired the Enkel Group, a construction company belonging to Abergo, who later managed to interest him in the project to build a CLT factory in Uruguay.
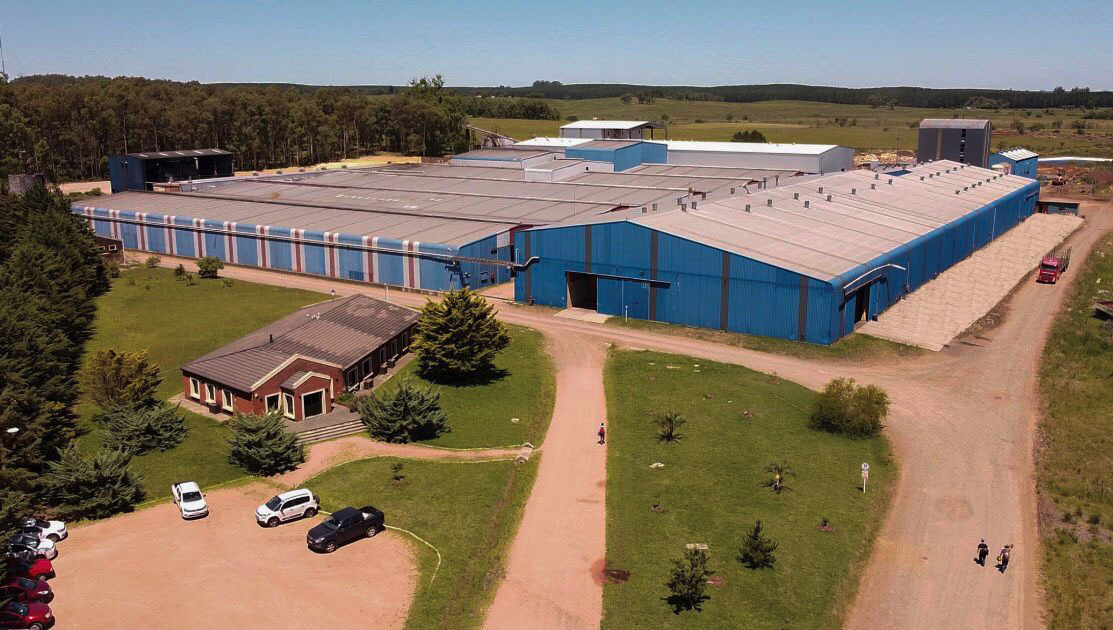
But why use imported materials? The panels are made with wood from young pine trees (of 10 to 15 years old), an existing resource in Uruguay, but one that is largely exported in logs, bringing little added value to the country’s economy.
Exports of roundwood pine in Uruguay grew 115% in 2021, almost double the increase in total timber exports (64%). Pine logs accounted for US$240 million out of a total of US$569 million in exported timber.
The installed capacity of domestic pine sawmills allows for the processing of between 3,000 and 4,000 hectares of mature forest per year. The area of pine plantations needed to meet this capacity is between 60,000 and 80,000 hectares; the nation’s total planted area is currently more than double the latter number.
Arboreal estimates that the nation’s volume of mature trees is more than enough to supply an industrial processing of 600,000 cubic metres of cut-to-size CLT boards per year – a production they aim to achieve in the short term, with 50-60% intended for the domestic market and the remainder for export.
A paradigm shift
Any “paradigm shift” towards timber construction is seen as complex by the industry. Julio Canarano, a member and advisor to the Association of Private Construction Developers of Uruguay (APPCU), said he sees the recent “roadmap” and changes that the Ministry of Housing is introducing on wood construction for social housing in a positive light.
However, Canarano said that “it has always been difficult for Uruguay to open up to alternative materials in construction because the industry is very traditionalist.” He gave as an example the nation’s slowness to incorporate the use of gypsum when it had already taken off elsewhere in the world.
Arboreal told Diálogo Chino that the market is beginning to move, with many clients making enquiries, and several architects interested in learning about the technique contacting the firm. It also recently participated in a construction fair for the first time, in Montevideo. The group sees it as necessary to create a critical mass, and inform both the sector and the public, because a preconception persists that “wood burns, moths and rots”.
According to APPCU, another challenge is training the country’s labour force. Arboreal plans to initially train 6,000 construction workers across the country to “switch from using a bucket with a mixture and a mason’s trowel to a laser leveller and automated tools,” Matías Abergo said in a recent interview.
It has always been difficult for Uruguay to open up to alternative materials in construction because the industry is very traditionalist
“This is like assembling a Lego without using force, everything is designed so that the walls are straight without effort, and the workers go home clean,” he added. The training cycle involves national universities such as the Universidad del Trabajo (UTU), the National Institute of Employment and Vocational Training (INEFOP) and the PIT-CNT, a national trade union centre.
Eduardo Burgos from the PIT-CNT told Diálogo Chino that they are interested in training workers and technicians, but also in learning about the system in order to assess whether it is viable to use it for housing construction by cooperatives. There is reportedly a deficit of between 60,000 and 70,000 homes in Uruguay, according to government officials.
“We have a fairly fluid dialogue with the company Arboreal, we are now budgeting for one of our cooperatives to see how much a square metre will cost,” said Burgos. The company estimates a standard price of around US$1,100 per square metre, according to the quote presented by Arboreal to the Ministry of Housing in a document this May.
The PIT-CNT also believes that “the production model cannot be to export logs, but to add value, knowledge and technology to these processes; we are advocates of non-traditional systems that make construction cheaper.”
Both the sawmill and the CLT plant, as well as the processes associated with the pine plantations and distribution of the materials, can generate jobs, according to both the company and the workers’ union.
A 2021 report on the forestry sector from Uruguay XXI, a government trade promotion agency, claimed that there an abundant availability of pine wood is assured for the next 20 years, with very large volume peaks in the near future: “An annual average of more than 3 million cubic metres that far exceeds Uruguay’s installed industrial capacity.”